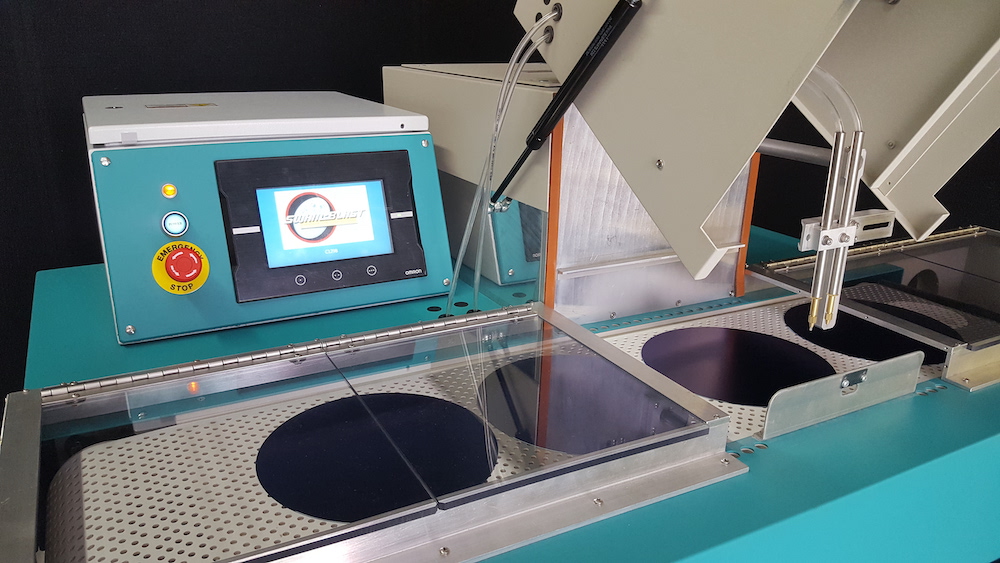
11 Apr Control Variable #5 of 5: Speeds and Feeds
In Micro Abrasive Processing, precision graded abrasive particles are introduced into a stream of compressed gas. The mixture is transported through a hose and then focused through a small nozzle aimed at the area to be processed.
This blog post describes the fifth variable that is critical to the micro sandblasting process – “Speeds and Feeds”. Speeds and Feeds control the amount of time the intended substrate is exposed to the abrasive blast thus controlling the material removal rate.
What makes Speeds and Feeds effective:
ONE: First Four Control Variables
- Abrasive powder – material properties, particle size and shape, consistency over large volumes, and over time.
- Blast pressure that decides velocity at which abrasive particles travel for micro sandblasting.
- Nozzles – material selected to manufacture the nozzle, diameter and shape of the nozzle, distance between the nozzle tip and target area to be processed.
- The ratio of the abrasive to the carrier gas in the stream.
TWO: Automation
Crystal Mark, Inc. has in house vertical manufacturing capabilities to design custom automated systems that provide precise control of speeds and feeds. From two axis conveyor systems and laths to 4, 5 or 6 axis nozzle positioning systems.
Important Note: If any one of the first four Control Variables changes during processing or from one production run to the next it will affect the output of the automated process. Thus it is important to control those first four variables and design in, as wide as is reasonable, a final acceptance criteria for the product to ensure a production robust process.
Example: SWAM® Belt Abrading System
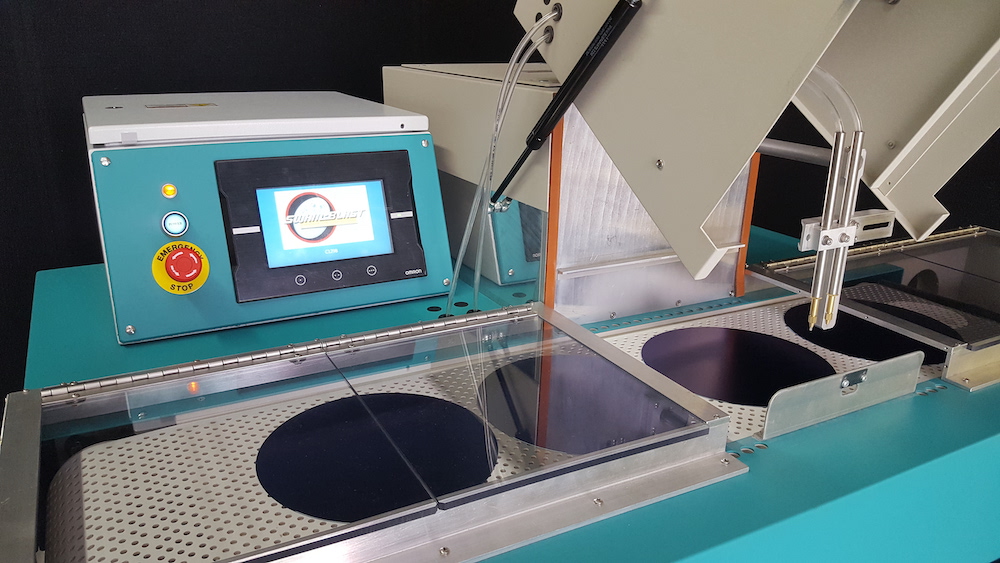
Control Variable # 5 with Micro Abrasive Blasting – Speeds and Feeds
A substrate to be processed is loaded manually or automatically onto a conveyor belt. This conveyor transports the substrate into the processing enclosure where one or more nozzles reciprocates over the substrate to provide precise and even exposure of the micro abrasive process. The target speeds and feeds of the belt and nozzle reciprocator are independently controlled with a simple and intuitive user interface.
Example: SWAM® Rotary Abrader Systems
Crystal Mark, Inc. offers options for single spindle system or dual spindle system as required for the application throughput.
With the rotary abrader systems, the rotary and linear motions can be independently controlled for the required speeds and feeds.
Example: SWAM® Model C-5100 Wafer Coring and Contouring System
The SWAM C-5100 system is designed for Wafer Coring and Edge-Rounding of silicon, silicon carbide, sapphire, germanium, GaAs, and other Semiconductor materials. The wafer orientation is precisely controlled on a rotary vacuum chuck; the nozzle position is programmed for the intended machining application. The SWAM C-5100 replaces a two stage process, laser cut then grinding operation with one CNC controlled micro abrasive system that cores and edge rounds at the same time. It also cuts flats and notches.
While automation enables precise control over speeds and feeds, the other four control variables, abrasive powder, pressure control, nozzles and abrasive to carrier ratio, play an instrumental role in achieving the predictive rate of removal. The versatile abrasive powder induction technology along with truly independent control of abrasive and carrier gas enables:
- Use of abrasives with particle sizes ranging from sub-micron levels up to 500 microns.
- Pressure of the stream ranging from 0.5 psi, to as high as 300 psi as required for an application.
- Vast selection of Nozzles: 0.005-0.125” round or 0.0065”square to 0.150 x 0.020” rectangular. (contact us for a standard nozzle list or to design a custom nozzle for specialty applications)
- The widest possible window of parameters available in the industry.
CONTROLLING A MICRO ABRASIVE PROCESS – FIVE VARIABLES:
FOUR: Abrasive to Carrier Ratio
FIVE: Speeds and Feeds